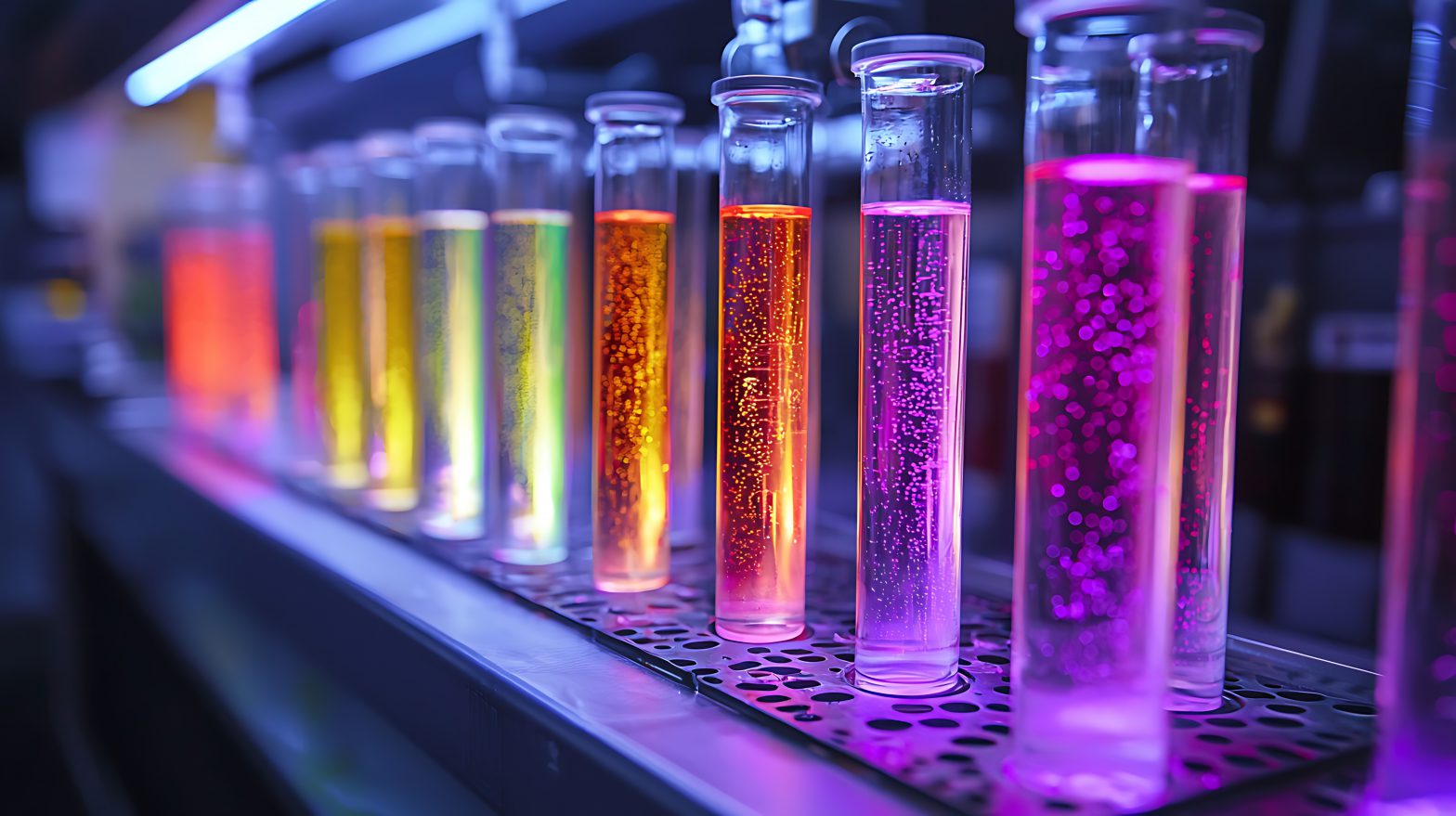
Understanding UV-A Irradiance, and Requirements for Various Applications
Home /
Blog /
Tech & Color Science /
Understanding UV-A Irradiance, and Requirements for Various Applications
Ultraviolet lights are indispensable tools for various specialty applications, ranging from industrial processes such as UV-curing of inks, adhesives, dies, all the way to UV fluorescence in the arts. It can be a challenge, however, to quantify and understand the amount and direction of UV emitted by a product, and whether or not it is sufficient, suitable, or excessive for a particular application.
In this article, we will go over the basics of how UV energy is quantified and measured, and provide some estimated UV-A irradiance values for various applications. We also go over how to interpret UV irradiance specifications.
Why Measuring UV is Difficult
As humans, we rely on our visual system to intuitively understand if a white light is "bright" or not. We might even rely on our vision to see bright sunshine on a summer day, and remember to put on some sunscreen before going out, even though our concern is with the invisible UV rays, and not the visible sunlight.
In fact, as humans, we are completely unable to visually detect the presence or intensity of UV rays. This makes measuring and quantifying UV that much more difficult, and we must rely on measurement devices to get an empirical reading, and of course not everyone has the budget to be purchasing expensive UV radiometry equipment. Compounding on this difficulty is that many UV lamp manufacturers do not provide detailed specifications on the UV output, making it almost impossible to meaningfully compare performance.
Despite the difficulty, a little bit of background on UV specifications can go a long way in ensuring you have the correct setup, and this can ultimately save you time, hassle and money. First, we'll go over the basic concepts of how UV is measured, and what the units of measurement mean.
How UV-A is Measured & Quantified
The most basic and useful way in which UV is characterized is via its irradiance value. Conceptually, irradiance tells us the amount of UV energy that falls on a particular surface, and is one of the primary determinants in whether the UV intensity is insufficient, sufficient, or excessive for a particular application.
One of the most common ways to measure UV irradiance is in watts per square meter (W/m²). An irradiance value of 5 watts per square meter, for example, tells us that a total of 5 watts of UV energy are falling across a one square meter area. The higher the irradiance, the higher the UV level. In a sense, you can also understand irradiance as the density of UV energy that falls on a surface.
Other common metrics include milliwatts per square centimeter (mW/cm²) and microwatts per square centimeter (µW/cm²). A microwatt is a one-thousandth of a milliwatt. Multiply the mW/m² value by 1000 to get the equivalent irradiance in µW/cm².
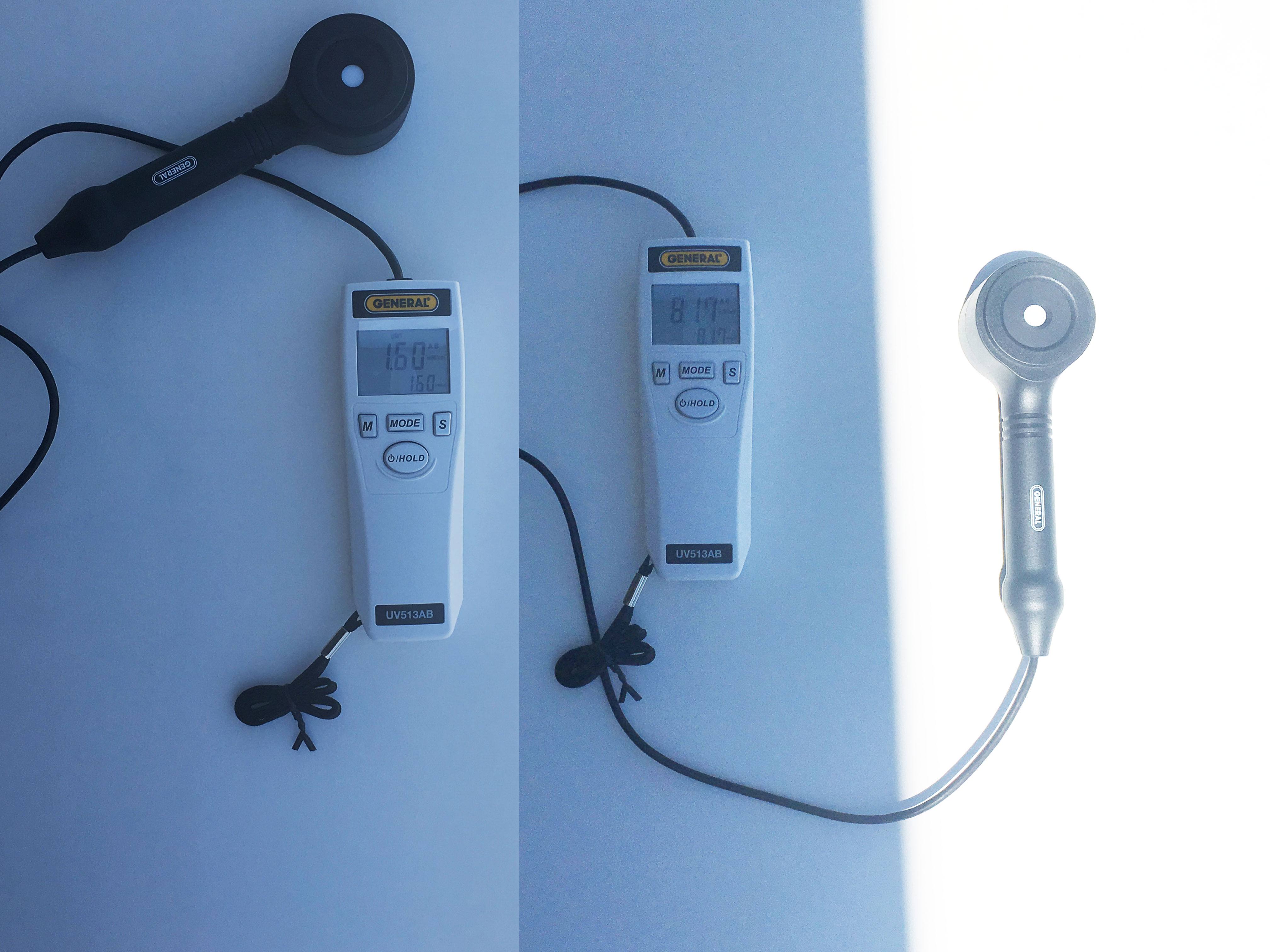
As a baseline frame of reference, noon sunshine provides upwards of 10 mW/cm², while indirect daylight will provide 1.0 - 2.0 mW/cm².
Keep in mind that the UV irradiance value is about how much UV energy falls on a particular surface point, and is not the same as how strong a particular UV lamp is. A 20W fluorescent blacklight that emits UV in all directions, for example, may provide lower UV irradiance at a particular spot than a 5W UV flashlight that focuses its UV output in a narrow beam.
How Much UV Irradiance?
The amount of UV irradiance needed depends on whether the intended application involves either fluorescence, or curing. Fluorescence applications rely on ultraviolet energy to induce fluorescence of various objects such as paints, dyes, minerals and other organic materials. Many of the "blacklight effects" rely on fluorescence. Curing, on the other hand, is a chemical process in which a material undergoes a physical change as a result of receiving a "dosage" of UV energy. Most industrial processes such as adhesives and resin curing fall under this category.
Because of the fundamental difference in the physics behind these two types of applications, the UV irradiance requirements also differ significantly.
For basic ultraviolet fluorescence effects, an irradiance value of 0.01 mW/cm² is typically sufficient to begin seeing fluorescence, and at values of 0.05 mW/cm², fluorescent colors really begin to pop.
For UV curing, UV irradiance needs vary by material and manufacturer, but are generally orders of magnitude higher than fluorescence applications. On the low end, you will need 5.0 mW/cm² to for initial curing (to fix into place), while on the higher end, you will need upwards of 50 mW/cm² or more.
Keep in mind that these are very general guidelines only, and the specific UV irradiance requirements will vary widely among products and manufacturers.
There are also considerations with respect to how much tolerance there is for UV-A irradiance in an application. In fluorescence applications, having insufficient UV irradiance may lead to objects not appearing as bright as you might like. On the other hand, insufficient UV irradiance for curing applications could mean slower cure times, or no curability whatsoever.
How To Determine if a UV Lamp is Strong Enough
We've so far discussed the UV-A irradiance needs from the perspective of the material subject to the UV rays. Next, we'll discuss understanding the UV irradiance specifications for UV lamp products and how to determine if they are sufficient for our application.
As we discussed earlier, UV irradiance is the metric that we care about, as it tells us how much UV energy falls on a particular point. This will then allow us to determine if that amount of UV energy is sufficient for our application.
While the power and UV output of a UV lamp is of course important, even more important is the orientation and distance of the UV lamp to the material in question. Distance is of particular interest due to the inverse-square-law of emitted light and UV rays - for every 2x increase in distance, irradiance decreases 4x fold.
Below are several examples of Waveform Lighting's UV LED products and how they can help determine the UV irradiance levels for various installation scenarios.
Our first example is the UV flashlight, which emits 365 nm UV light in a narrow beam of only 12 degrees. The chart below shows the irradiance values as measured at various points along the axis of the UV beam, in 1-ft intervals.
At a relatively close 12" distance from the flashlight, irradiance values of 29.5 mW/cm² were measured. This is high enough for many UV curing applications, although the narrow beam angle may render this useful primarily for spot-curing applications only. You will also see that as the distance increases, so does the UV irradiance values, and that the inverse-square-law generally holds. By the time we reach 48" from the light source, we only get a 2.1 mW/cm² UV irradiance value.
In our second example, we look at the 20W 365 nm UV flood light. As its name suggests, the flood light emits light in a "flood" pattern, which is a much wider beam than a narrow-beam flashlight.
The graphic below shows the general setup for measuring UV irradiance across various points along the surface upon which the UV flood light projects. You will see there are two distance components that determine the UV irradiance - the first being the perpendicular distance away from the lamp, and the second being the distance from the center of the beam pattern.
As we saw with the UV flashlight example above, moving further away from the UV lamp will result in a reduction in UV irradiance. For the UV flood lamp, we publish a separate chart for each of the various distances from the lamp.
Below is the chart for the UV irradiance pattern at a perpendicular distance of 6 feet from the UV lamp. At the very center of the beam, we measure a UV irradiance value of 23 µW/cm². The radial rings show the distance from this center point, and the various UV irradiance values measured within each square.
From this chart, we can conclude that the UV flood light mounted at a distance of 6 ft, can cover an approximately 20 sq ft area with 11+ µW/cm² of UV irradiance, sufficient for basic fluorescence effects, but at this mounting height, most likely not for UV curing applications.
Beware of Incorrect Wavelengths!
So far, we've discussed the quantity of UV-A irradiance, but not necessarily the quality of it. In looking at UV-A quality, we are primarily concerned with wavelength.
UV-A radiation is broadly defined as any type of electromagnetic radiation whose wavelengths are between 320 nm and 400 nm. All wavelengths within this range fall under the UV-A definition, but not all wavelengths are as effective at creating fluorescence effects or initiating curing processes. Mercury and fluorescent black lights tend to emit in a wide range of wavelengths, but one of the primary wavelengths that they emit at is 365 nm.
As a result, many products are either designed / optimized, or at the very least characterized, around 365 nm irradiance levels. Let's say a UV curing adhesive you purchased calls for 20 mW/cm² at 365 nm. If your UV LED has a wavelength of 395 nm, for example, irradiance values are almost meaningless, because the adhesive is characterized at 365 nm, and not 395 nm. This is similar to designing a lamp with visible light of the wrong color - the intensity does not really matter because the color is off in the first place.
Final Thoughts
Finding the correct UV lamp for a UV-A application may seem like a daunting task at first, but can definitely be conquered step-by-step. First, get a rough estimate on the UV irradiance values needed for your application, depending on the application. Many fluorescence effects will happen at low UV irradiance values, but UV-based curing may need much more.
Next, find a UV lamp product from a reputable supplier that provides reliable UV irradiance data. The data should specify distance from the lamp, as this is just as important as the power rating of the lamp itself.
Finally, ensure that the UV lamp emits the correct wavelength. Many LED-based UV lamps claim to emit UV light, when in fact much of the energy is near the tail end of UV-A, bordering on visible violet light.
If you're able to check off these three basic guidelines, you should be well on your way to finding a suitable UV solution for your project!
In this article, we will go over the basics of how UV energy is quantified and measured, and provide some estimated UV-A irradiance values for various applications. We also go over how to interpret UV irradiance specifications.
Why Measuring UV is Difficult
As humans, we rely on our visual system to intuitively understand if a white light is "bright" or not. We might even rely on our vision to see bright sunshine on a summer day, and remember to put on some sunscreen before going out, even though our concern is with the invisible UV rays, and not the visible sunlight.
In fact, as humans, we are completely unable to visually detect the presence or intensity of UV rays. This makes measuring and quantifying UV that much more difficult, and we must rely on measurement devices to get an empirical reading, and of course not everyone has the budget to be purchasing expensive UV radiometry equipment. Compounding on this difficulty is that many UV lamp manufacturers do not provide detailed specifications on the UV output, making it almost impossible to meaningfully compare performance.
Despite the difficulty, a little bit of background on UV specifications can go a long way in ensuring you have the correct setup, and this can ultimately save you time, hassle and money. First, we'll go over the basic concepts of how UV is measured, and what the units of measurement mean.
How UV-A is Measured & Quantified
The most basic and useful way in which UV is characterized is via its irradiance value. Conceptually, irradiance tells us the amount of UV energy that falls on a particular surface, and is one of the primary determinants in whether the UV intensity is insufficient, sufficient, or excessive for a particular application.
One of the most common ways to measure UV irradiance is in watts per square meter (W/m²). An irradiance value of 5 watts per square meter, for example, tells us that a total of 5 watts of UV energy are falling across a one square meter area. The higher the irradiance, the higher the UV level. In a sense, you can also understand irradiance as the density of UV energy that falls on a surface.
Other common metrics include milliwatts per square centimeter (mW/cm²) and microwatts per square centimeter (µW/cm²). A microwatt is a one-thousandth of a milliwatt. Multiply the mW/m² value by 1000 to get the equivalent irradiance in µW/cm².
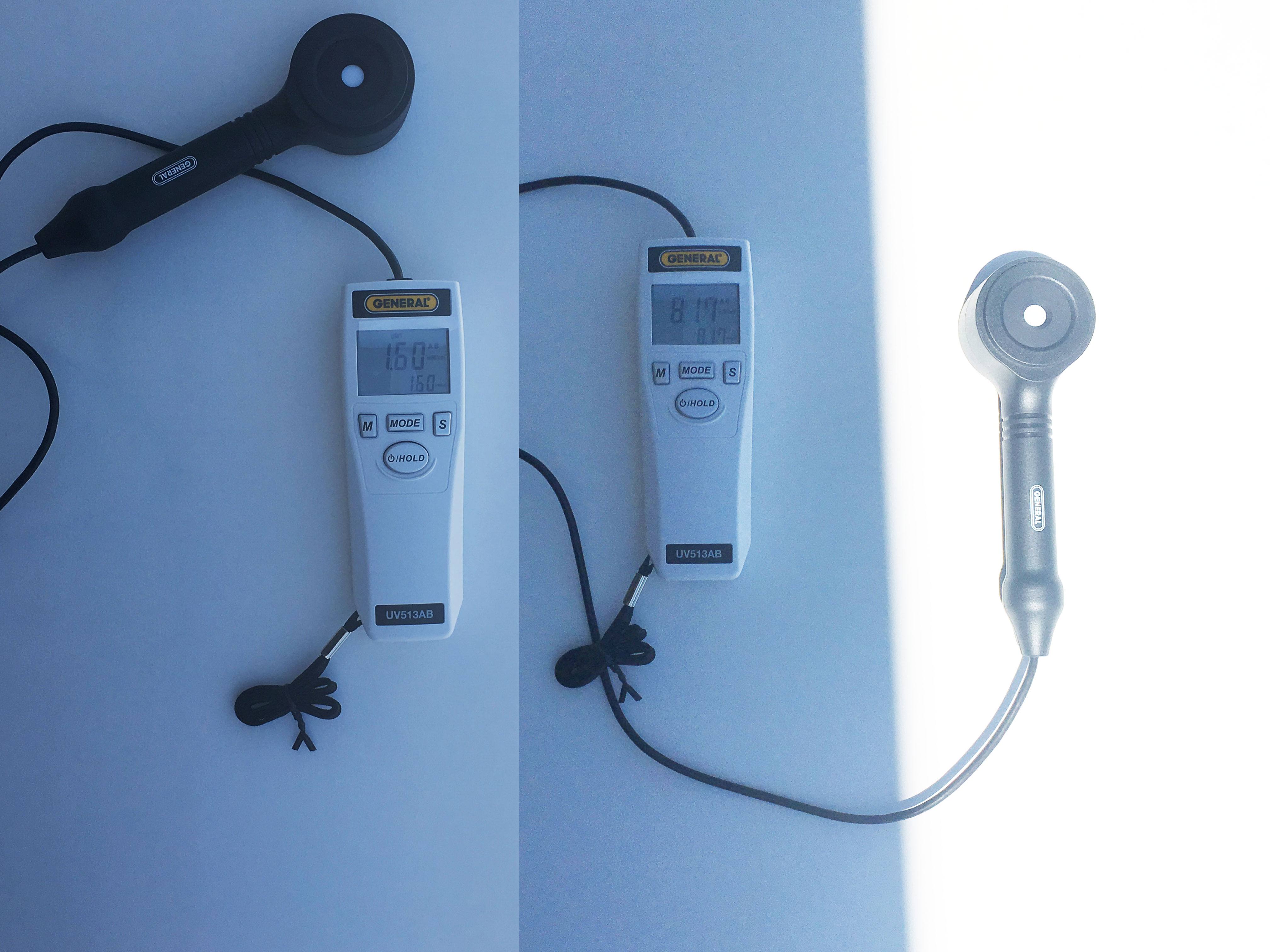
As a baseline frame of reference, noon sunshine provides upwards of 10 mW/cm², while indirect daylight will provide 1.0 - 2.0 mW/cm².
Keep in mind that the UV irradiance value is about how much UV energy falls on a particular surface point, and is not the same as how strong a particular UV lamp is. A 20W fluorescent blacklight that emits UV in all directions, for example, may provide lower UV irradiance at a particular spot than a 5W UV flashlight that focuses its UV output in a narrow beam.
How Much UV Irradiance?
The amount of UV irradiance needed depends on whether the intended application involves either fluorescence, or curing. Fluorescence applications rely on ultraviolet energy to induce fluorescence of various objects such as paints, dyes, minerals and other organic materials. Many of the "blacklight effects" rely on fluorescence. Curing, on the other hand, is a chemical process in which a material undergoes a physical change as a result of receiving a "dosage" of UV energy. Most industrial processes such as adhesives and resin curing fall under this category.
Because of the fundamental difference in the physics behind these two types of applications, the UV irradiance requirements also differ significantly.
For basic ultraviolet fluorescence effects, an irradiance value of 0.01 mW/cm² is typically sufficient to begin seeing fluorescence, and at values of 0.05 mW/cm², fluorescent colors really begin to pop.
For UV curing, UV irradiance needs vary by material and manufacturer, but are generally orders of magnitude higher than fluorescence applications. On the low end, you will need 5.0 mW/cm² to for initial curing (to fix into place), while on the higher end, you will need upwards of 50 mW/cm² or more.
Keep in mind that these are very general guidelines only, and the specific UV irradiance requirements will vary widely among products and manufacturers.
There are also considerations with respect to how much tolerance there is for UV-A irradiance in an application. In fluorescence applications, having insufficient UV irradiance may lead to objects not appearing as bright as you might like. On the other hand, insufficient UV irradiance for curing applications could mean slower cure times, or no curability whatsoever.
How To Determine if a UV Lamp is Strong Enough
We've so far discussed the UV-A irradiance needs from the perspective of the material subject to the UV rays. Next, we'll discuss understanding the UV irradiance specifications for UV lamp products and how to determine if they are sufficient for our application.
As we discussed earlier, UV irradiance is the metric that we care about, as it tells us how much UV energy falls on a particular point. This will then allow us to determine if that amount of UV energy is sufficient for our application.
While the power and UV output of a UV lamp is of course important, even more important is the orientation and distance of the UV lamp to the material in question. Distance is of particular interest due to the inverse-square-law of emitted light and UV rays - for every 2x increase in distance, irradiance decreases 4x fold.
Below are several examples of Waveform Lighting's UV LED products and how they can help determine the UV irradiance levels for various installation scenarios.
Our first example is the UV flashlight, which emits 365 nm UV light in a narrow beam of only 12 degrees. The chart below shows the irradiance values as measured at various points along the axis of the UV beam, in 1-ft intervals.
At a relatively close 12" distance from the flashlight, irradiance values of 29.5 mW/cm² were measured. This is high enough for many UV curing applications, although the narrow beam angle may render this useful primarily for spot-curing applications only. You will also see that as the distance increases, so does the UV irradiance values, and that the inverse-square-law generally holds. By the time we reach 48" from the light source, we only get a 2.1 mW/cm² UV irradiance value.
In our second example, we look at the 20W 365 nm UV flood light. As its name suggests, the flood light emits light in a "flood" pattern, which is a much wider beam than a narrow-beam flashlight.
The graphic below shows the general setup for measuring UV irradiance across various points along the surface upon which the UV flood light projects. You will see there are two distance components that determine the UV irradiance - the first being the perpendicular distance away from the lamp, and the second being the distance from the center of the beam pattern.
As we saw with the UV flashlight example above, moving further away from the UV lamp will result in a reduction in UV irradiance. For the UV flood lamp, we publish a separate chart for each of the various distances from the lamp.
Below is the chart for the UV irradiance pattern at a perpendicular distance of 6 feet from the UV lamp. At the very center of the beam, we measure a UV irradiance value of 23 µW/cm². The radial rings show the distance from this center point, and the various UV irradiance values measured within each square.
From this chart, we can conclude that the UV flood light mounted at a distance of 6 ft, can cover an approximately 20 sq ft area with 11+ µW/cm² of UV irradiance, sufficient for basic fluorescence effects, but at this mounting height, most likely not for UV curing applications.
Beware of Incorrect Wavelengths!
So far, we've discussed the quantity of UV-A irradiance, but not necessarily the quality of it. In looking at UV-A quality, we are primarily concerned with wavelength.
UV-A radiation is broadly defined as any type of electromagnetic radiation whose wavelengths are between 320 nm and 400 nm. All wavelengths within this range fall under the UV-A definition, but not all wavelengths are as effective at creating fluorescence effects or initiating curing processes. Mercury and fluorescent black lights tend to emit in a wide range of wavelengths, but one of the primary wavelengths that they emit at is 365 nm.
As a result, many products are either designed / optimized, or at the very least characterized, around 365 nm irradiance levels. Let's say a UV curing adhesive you purchased calls for 20 mW/cm² at 365 nm. If your UV LED has a wavelength of 395 nm, for example, irradiance values are almost meaningless, because the adhesive is characterized at 365 nm, and not 395 nm. This is similar to designing a lamp with visible light of the wrong color - the intensity does not really matter because the color is off in the first place.
Final Thoughts
Finding the correct UV lamp for a UV-A application may seem like a daunting task at first, but can definitely be conquered step-by-step. First, get a rough estimate on the UV irradiance values needed for your application, depending on the application. Many fluorescence effects will happen at low UV irradiance values, but UV-based curing may need much more.
Next, find a UV lamp product from a reputable supplier that provides reliable UV irradiance data. The data should specify distance from the lamp, as this is just as important as the power rating of the lamp itself.
Finally, ensure that the UV lamp emits the correct wavelength. Many LED-based UV lamps claim to emit UV light, when in fact much of the energy is near the tail end of UV-A, bordering on visible violet light.
If you're able to check off these three basic guidelines, you should be well on your way to finding a suitable UV solution for your project!
Other Posts
Browse Waveform Lighting Products
A-Series LED Bulbs
Our A19 and A21 lamps fit in standard lamp fixtures and are perfect for floor and desk lamp fixtures.
Candelabra LED Bulbs
Our candelabra LED bulbs offer soft and warm light output in a decorative bulb style that fits E12 lamp fixtures.
BR30 LED Lamps
BR30 lamps are ceiling lamps that fit in residential and commercial fixtures with 4-inch or wider openings.