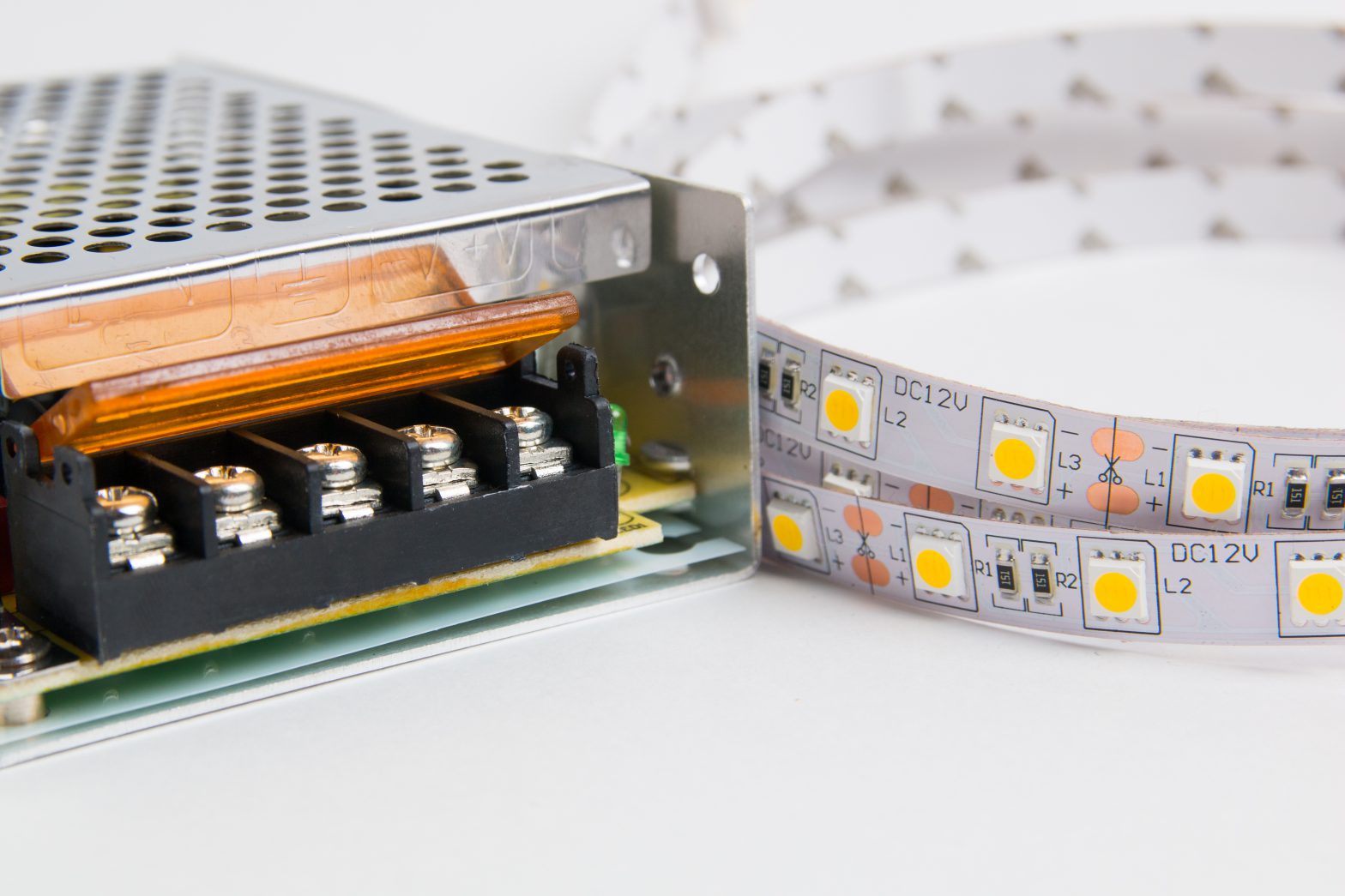
Advantages of a 24V LED system vs 12V
If you are considering purchasing lights for or installing a low voltage lighting system, you will likely have come across both 12V DC and 24V DC options. Oftentimes, the price and performance specifications listed will be the same, and you may be wondering, "what's the difference? Which one should I choose?"
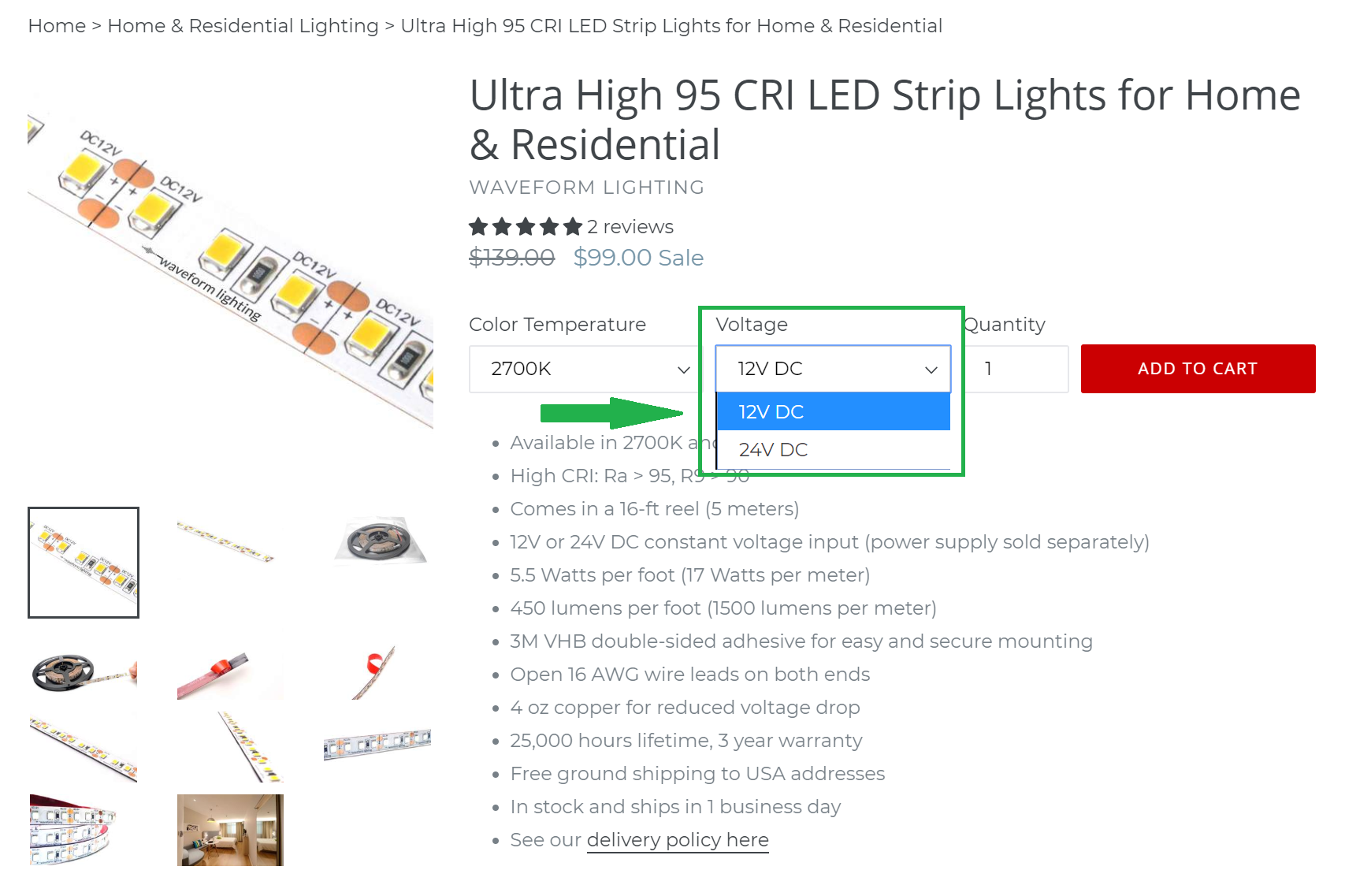
Waveform Lighting's LED strips, for example, are available in both 12V DC and 24V DC.
In general, the difference between 12V DC and 24V DC is not extremely significant as long as the correct accessories (e.g. power supplies) are chosen.
If you're new to LED strip lights, we recommend choosing 12V DC, because of the shorter distance between cut-line intervals (1 inch for 12V vs 2 inches for 24V). This gives you more flexibility in cutting the LED strips to your desired length.
If you're looking for maximum efficiency, we recommend choosing 24V DC, because of its lowered potential for voltage drop.
If you're curious to learn more about the technical aspects, read below for more differences:
Despite some of the most popular power supply voltage options being 12V or 24V DC, it's important to remember that (most) individual LEDs are actually 3V DC devices. It is through configuring the LEDs in a particular parallel vs series combination, that the voltage of an LED system can be made to match a particular power supply voltage.
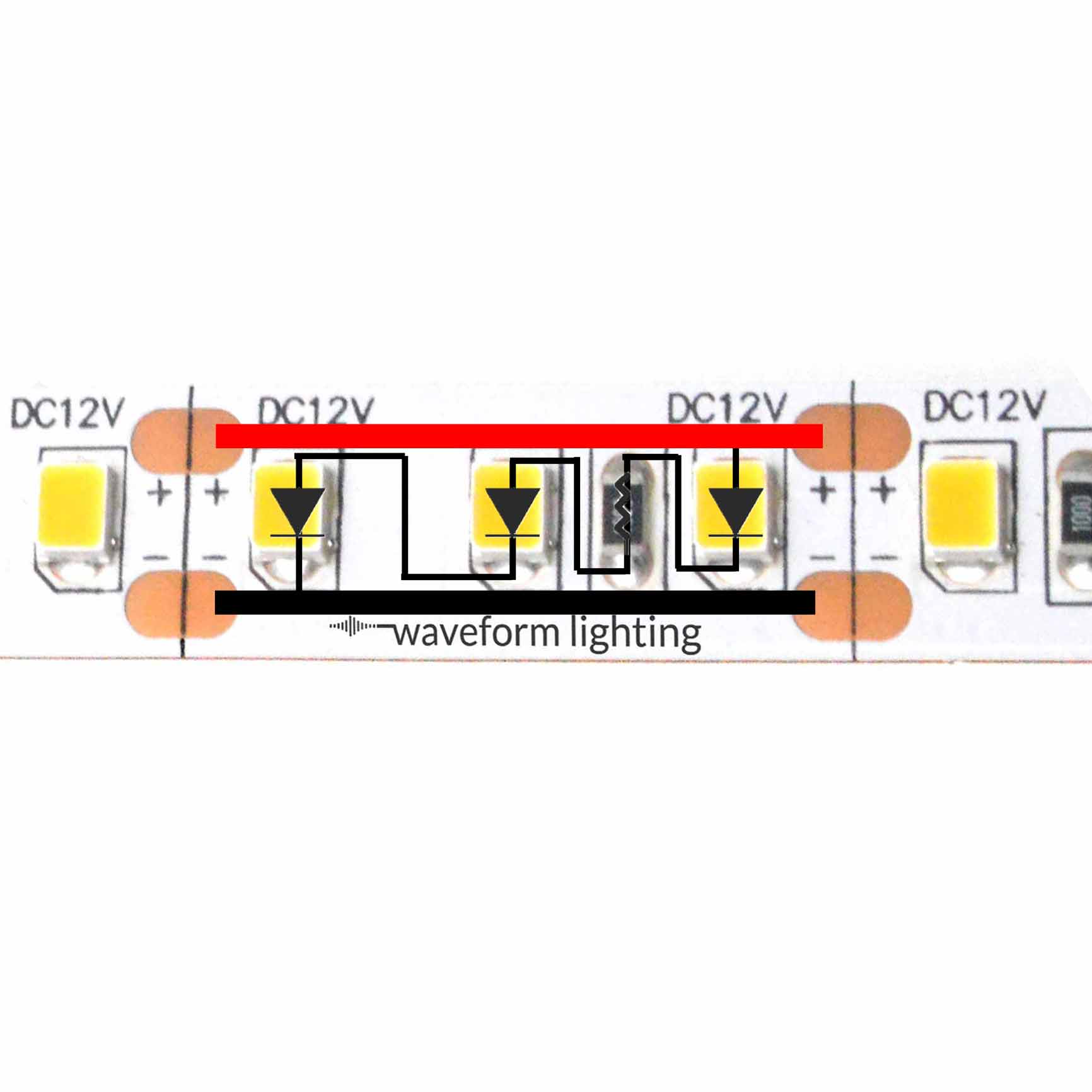
Typically, a 12V LED strip is configured with 3 LEDs in series per string. At 3V each, the total LED voltage is only 9V, or about 75% of the total voltage. The remaining voltage is dissipated by a current limiting resistor. Since the resistor does not contribute to illumination, we can conclude that in a 12V LED strip, approximately 25% of the electrical energy is dissipated as waste heat.
In a 24V LED system, there is typically enough voltage overhead to allow for 7 LEDs in series per string. At 3V each, the total LED voltage is 21V, or about 88% of the 24V input. In this situation, less than 13% of the voltage energy is wasted as heat energy.
In short, a 24V LED system can actually reduce inherent electrical design inefficiencies by more than 50%.
Waveform Lighting's ABSOLUTE SERIES LED modules, for example, take advantage of this fact and utilize 5 parallel strings of 7 LEDs in series each to achieve a 24V, 35 LED PCB layout.
Electrical power is determined by the equation P = V x I. To maintain the same power (P), if voltage (V) goes up, current (I) must come down by a proportional amount.
As a concrete example, if we keep 48W as our target output, a 12V system will require 4 Amps (12V x 4A = 48W), while a 24V system will only require 2 Amps (24V x 2A = 48W).
Simply put, a 24V LED system will draw half the amount of current as a 12V LED system to achieve the same power level.
Why is this important?
Total current, rather than voltage, determines the thickness and width of copper conductors needed to safely transfer power.
If excessive amounts of current are forced through a small or narrow copper conductor, resistance inside the conductor itself will begin to become significant, and contribute to voltage drop and heat generation. In very extreme cases, this can even lead to electrical fires.
All else equal, a 24V LED system can get away with half of the electrical conductor requirements. You can use our voltage drop calculator to make sure you are still using sufficient conductor gauge for your LED strip projects.
Similar to conductor size, power supply size is also determined primarily by current rather than voltage. Part of this is also influenced by the physics relationship between electrical current and conductor size needs, as much of the internal wiring of a power supply unit is comprised of copper wiring.
Power supply size can be important when working with projects such as LED strip lights in under cabinet installations where there may be space constraints.
In applications such as LED strip lighting, the maximum continuous length of an LED strip is typically dictated by the electrical current that the LED strip copper traces can handle. Therefore, 24V LED strips will typically be able to handle twice the length that a 12V LED strip would, assuming that the power ratings of the two products are the same.
This is true for products beyond LED strips that also have daisy chaining capability.
For example, Waveform Lighting's LED strips have a specified max run length the differs depending on voltage: 16-ft (5 meters) for 12V, and 33-ft (10 meters) for 24V.
The difference between 12V and 24V is typically insignificant, but if you truly do not have a strong preference for one over the other, hopefully this article has convinced you of the benefits of a 24V system!
Read next: 12V systems have some advantages, too! Read our article about the pros and cons of 12V systems.
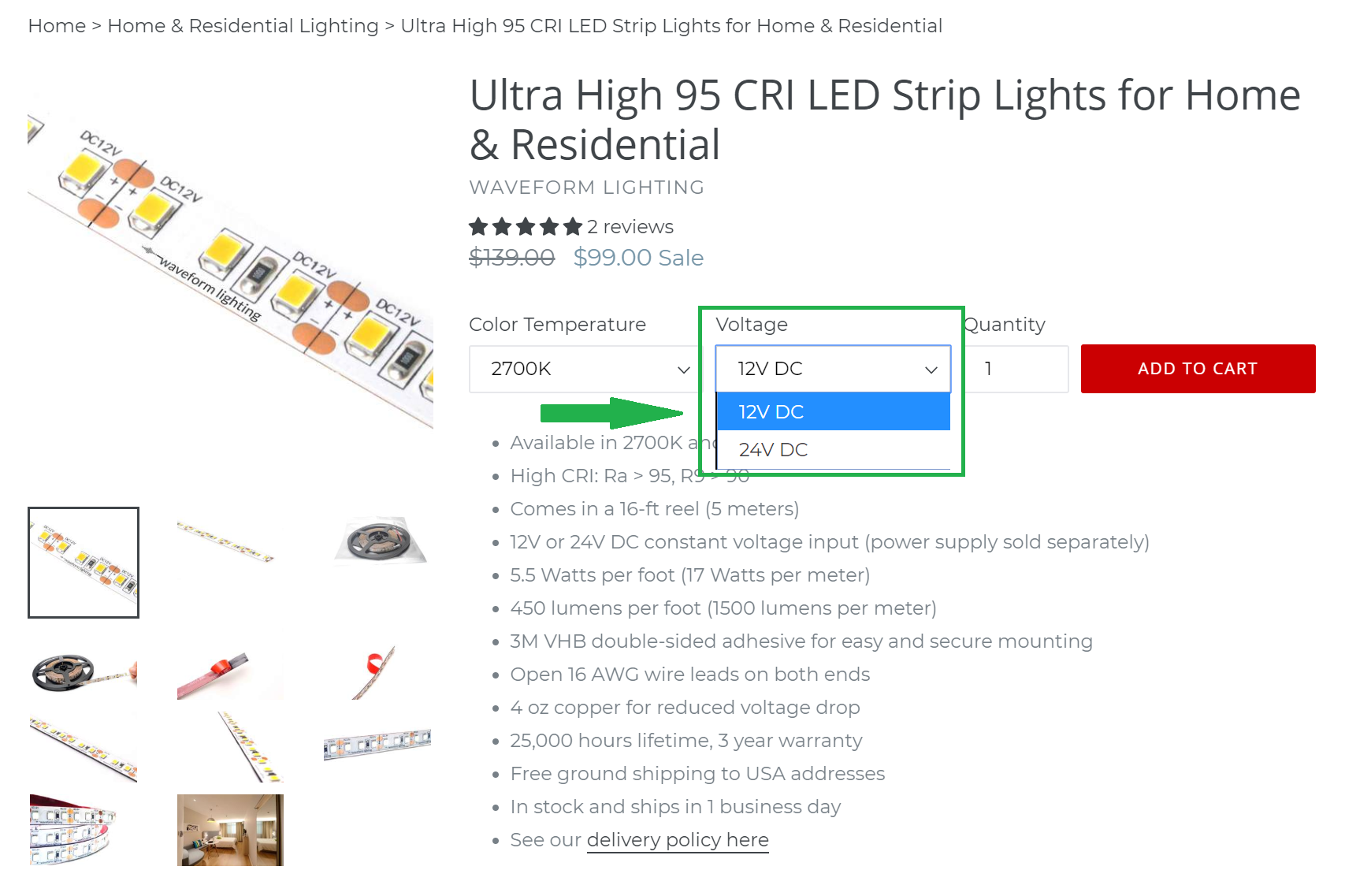
Waveform Lighting's LED strips, for example, are available in both 12V DC and 24V DC.
In general, the difference between 12V DC and 24V DC is not extremely significant as long as the correct accessories (e.g. power supplies) are chosen.
If you're new to LED strip lights, we recommend choosing 12V DC, because of the shorter distance between cut-line intervals (1 inch for 12V vs 2 inches for 24V). This gives you more flexibility in cutting the LED strips to your desired length.
If you're looking for maximum efficiency, we recommend choosing 24V DC, because of its lowered potential for voltage drop.
If you're curious to learn more about the technical aspects, read below for more differences:
1. 24V is better suited for LEDs.
Despite some of the most popular power supply voltage options being 12V or 24V DC, it's important to remember that (most) individual LEDs are actually 3V DC devices. It is through configuring the LEDs in a particular parallel vs series combination, that the voltage of an LED system can be made to match a particular power supply voltage.
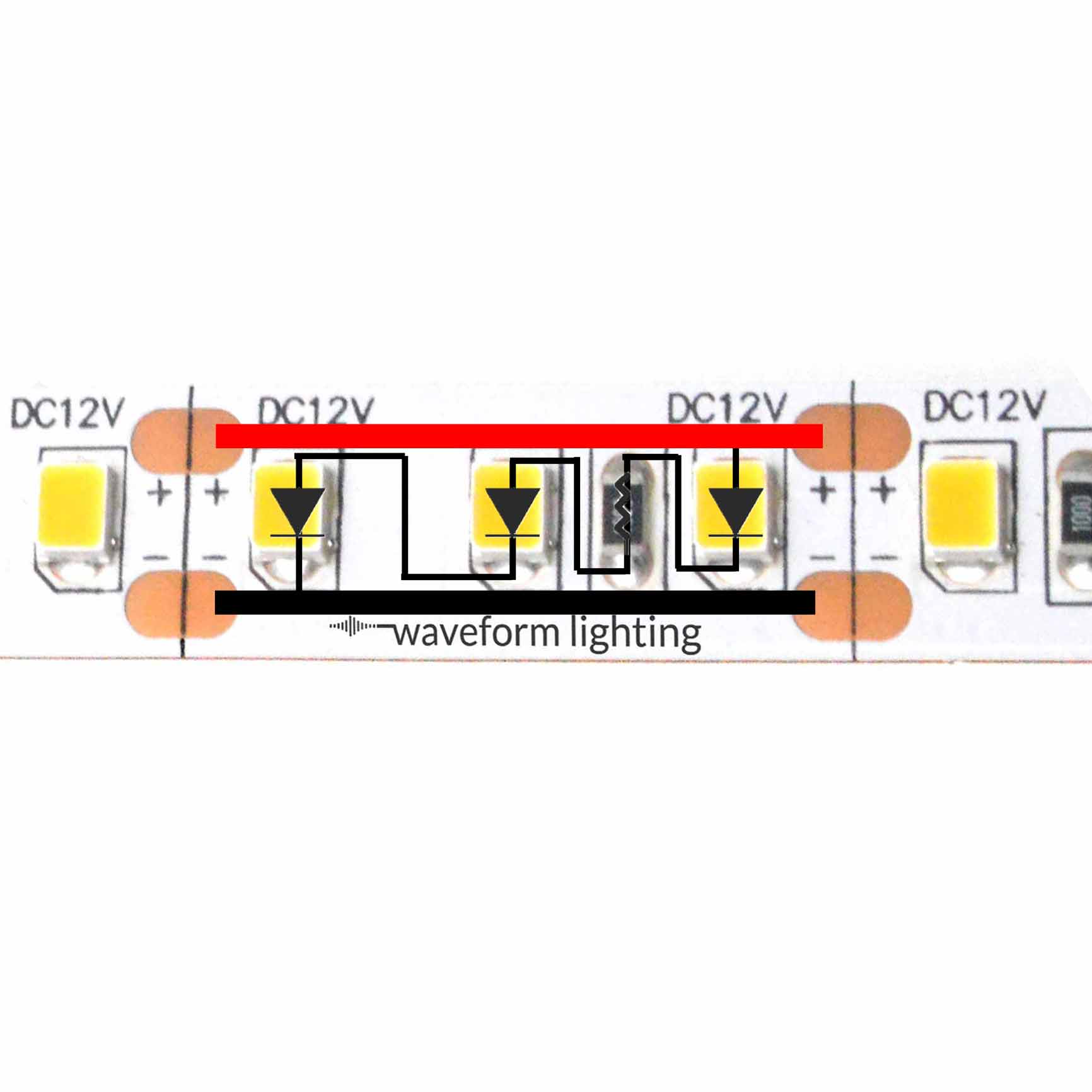
Typically, a 12V LED strip is configured with 3 LEDs in series per string. At 3V each, the total LED voltage is only 9V, or about 75% of the total voltage. The remaining voltage is dissipated by a current limiting resistor. Since the resistor does not contribute to illumination, we can conclude that in a 12V LED strip, approximately 25% of the electrical energy is dissipated as waste heat.
In a 24V LED system, there is typically enough voltage overhead to allow for 7 LEDs in series per string. At 3V each, the total LED voltage is 21V, or about 88% of the 24V input. In this situation, less than 13% of the voltage energy is wasted as heat energy.
In short, a 24V LED system can actually reduce inherent electrical design inefficiencies by more than 50%.
Waveform Lighting's ABSOLUTE SERIES LED modules, for example, take advantage of this fact and utilize 5 parallel strings of 7 LEDs in series each to achieve a 24V, 35 LED PCB layout.
2. 24V requires less conductor gauge.
Electrical power is determined by the equation P = V x I. To maintain the same power (P), if voltage (V) goes up, current (I) must come down by a proportional amount.
As a concrete example, if we keep 48W as our target output, a 12V system will require 4 Amps (12V x 4A = 48W), while a 24V system will only require 2 Amps (24V x 2A = 48W).
Simply put, a 24V LED system will draw half the amount of current as a 12V LED system to achieve the same power level.
Why is this important?
Total current, rather than voltage, determines the thickness and width of copper conductors needed to safely transfer power.
If excessive amounts of current are forced through a small or narrow copper conductor, resistance inside the conductor itself will begin to become significant, and contribute to voltage drop and heat generation. In very extreme cases, this can even lead to electrical fires.
All else equal, a 24V LED system can get away with half of the electrical conductor requirements. You can use our voltage drop calculator to make sure you are still using sufficient conductor gauge for your LED strip projects.
3. Smaller power supplies.
Similar to conductor size, power supply size is also determined primarily by current rather than voltage. Part of this is also influenced by the physics relationship between electrical current and conductor size needs, as much of the internal wiring of a power supply unit is comprised of copper wiring.
Power supply size can be important when working with projects such as LED strip lights in under cabinet installations where there may be space constraints.
4. Longer linear runs.
In applications such as LED strip lighting, the maximum continuous length of an LED strip is typically dictated by the electrical current that the LED strip copper traces can handle. Therefore, 24V LED strips will typically be able to handle twice the length that a 12V LED strip would, assuming that the power ratings of the two products are the same.
This is true for products beyond LED strips that also have daisy chaining capability.
For example, Waveform Lighting's LED strips have a specified max run length the differs depending on voltage: 16-ft (5 meters) for 12V, and 33-ft (10 meters) for 24V.
Bottom Line
The difference between 12V and 24V is typically insignificant, but if you truly do not have a strong preference for one over the other, hopefully this article has convinced you of the benefits of a 24V system!
Read next: 12V systems have some advantages, too! Read our article about the pros and cons of 12V systems.
Other Posts
Browse Waveform Lighting Products
A-Series LED Bulbs
Our A19 and A21 lamps fit in standard lamp fixtures and are perfect for floor and desk lamp fixtures.
Candelabra LED Bulbs
Our candelabra LED bulbs offer soft and warm light output in a decorative bulb style that fits E12 lamp fixtures.
BR30 LED Lamps
BR30 lamps are ceiling lamps that fit in residential and commercial fixtures with 4-inch or wider openings.